Volvo Fault Codes Manual
Volvo 850 service & repair manual TESTS W/CODES 1995 Volvo 850 1995 ENGINE PERFORMANCE Volvo – Self-Diagnostics INTRODUCTION If no faults were found while performing procedures in the F – BASIC TESTING article, proceed with self-diagnostics. If no fault codes are present, proceed to the H – TESTS W/O CODES article for diagnosis by symptom (i.e., ROUGH IDLE, NO START, etc.). NOTE: All voltage tests should be performed using a Digital Volt-Ohmmeter (DVOM) with a minimum 10-megohm input impedance, unless stated otherwise in testing procedures. SELF-DIAGNOSTIC SYSTEM RETRIEVING CODES CAUTION: Self-diagnostics for fuel injection and ignition systems are separate.
Use proper information for system being diagnosed. Fuel Injection & Ignition Systems Each system features a self-diagnostic function for fault tracing. Codes are retrieved using diagnostic unit “A” located in engine compartment, in front of right strut tower. Diagnostic unit “A” is equipped with an LED indicator, activation button and function selector cable. NOTE: Diagnostic unit “B” is not used for engine performance applications.
1: Identifying Diagnostic Unit “A” Courtesy of Volvo Cars of North America. Diagnostic unit “A” output socket No. 2 is used for fuel injection diagnosis, and socket No.
6 is used for ignition system diagnosis. Once function selector cable has been inserted in correct socket, depress button and keep depressed for more than one second (but not more than 3 seconds). Observe LED and count number of flashes to determine diagnostic trouble code, as faults stored in Electronic Control Unit (ECU) memory are read by observing LED flashes. If LED does not flash, see DIAGNOSTIC UNIT “A” LED DOES NOT FLASH. Diagnostic systems for fuel injection and ignition each store 13 codes. All codes contain 3 digits (example: 4-1-3).
Since all codes have 3 digits, each code requires 3 series of flashes. A 3-second interval separates each series of flashes.
See the appropriate TROUBLE CODE DEFINITION table. TROUBLE CODE IDENTIFICATION TROUBLE CODE DEFINITION – FUEL INJECTION SYSTEM (1) Code Fault/Repair 1-1-1. No Fault 1-1-2. Replace ECU 1-1-3 HO2S Integrator At Maximum Enrichment 1-2-1 MAF Sensor Signal Absent Or Faulty 1-2-3 Engine Temperature Sensor Signal Absent Or Faulty 1-3-1. Ignition System Speed Signal Absent Or Faulty 1-3-2.
Battery Voltage Too High Or Too Low 2-1-2. HO2S Sensor Signal Absent Or Faulty 2-2-1. Adaptive HO2S Control, Engine Running Too Rich At Part Load 2-2-3. IAC Valve Signal Absent Or Faulty 2-3-1. Adaptive HO2S Control, Engine Running Too Lean At Part Load 2-3-2. Adaptive HO2S Control, Provides Richer Mixture At Idle 3-1-1.
Speedometer Signal Absent Or Faulty 4-1-1. Throttle Switch Signal Absent Or Faulty 5-1-1. Adaptive HO2S Control, Provides Leaner Mixture At Idle 5-1-2.
HO2S Integrator At Maximum Lean Running Limit (1) – See FUEL INJECTION DIAGNOSIS under DIAGNOSTIC TROUBLE CODE TESTING for fault code diagnosis. TROUBLE CODE DEFINITION – IGNITION SYSTEM (1) Code Fault/Repair 1-1-1. No Faults 1-1-2. Replace ECU 1-2-3. Signal From Fuel Injection Absent Or Faulty 1-3-1.
VSS Signal Absent 1-4-3. Front Knock Sensor Signal Absent Or Faulty 1-4-4. Load Signal From Fuel Injection Absent Or Faulty 1-5-4. EGR System Leakage 2-1-4. VSS Signal Intermittent 2-4-1.
EGR Flow Incorrect 3-1-1. Speedometer Signal Absent Or Faulty 3-1-4. Camshaft Position Sensor Signal Absent Or Faulty 3-2-4 Camshaft Signal Intermittent 4-1-1. Throttle Switch Signal From Fuel Injection Absent Or Faulty 4-1-3.
EGR Temperature Sensor Signal Incorrect/Missing 4-3-2. High Temperature Warning In ECU Box 4-3-3. Rear Knock Sensor Signal Absent Or Faulty 5-1-3. High Temperature Warning In ECU Box (1) – See IGNITION SYSTEM DIAGNOSIS under DIAGNOSTIC TROUBLE CODE TESTING for fault code diagnosis. DIAGNOSTIC UNIT “A” LED DOES NOT FLASH 1) Disconnect diagnostic unit “A”. Turn ignition on.

Check for voltage at diagnostic connector terminal No. If voltage is not present, check fuse and wiring. If voltage is present, turn ignition off. 2) Connect an ohmmeter between diagnostic connector socket No. 8 and ground. Ohmmeter should indicate approximately zero ohms.
If reading is not approximately zero ohms, check wiring. If wiring is okay, replace diagnostic unit “A”. DIAGNOSTIC UNIT “A” LED FLASHES BUT ECU DOES NOT RESPOND 1) Turn ignition on. Check for voltage at diagnostic socket No.
2 (fuel injection system) or No. 6 (ignition system). Approximately 10 volts should be present. If approximately 10 volts is not present, check wiring. 2) Turn ignition off. Connect Measuring Unit (9813190). See MEASURING UNIT.
Connect an ohmmeter between socket No. 2 (fuel injection system) or No. 6 (ignition system) and measuring unit terminal No. If continuity is present, repeat test using a known good ECU.
CLEARING CODES 1) Turn ignition on. Press test button for more than 5 seconds. Release button. LED should light after 3 seconds.
Press button again for more than 5 seconds. Release button. LED should go out. 2) To ensure codes have been cleared, press button for more than one second (but no more than 3 seconds). If Code 1-1-1 is displayed, codes have been cleared. If codes have not been cleared, repeat procedure.
ECU LOCATION Fuel injection and ignition system ECUs are located in right front of engine compartment, in front of strut tower. MEASURING UNIT Connecting Measuring Unit (9813190) & Adapter (9813195) 1) Disconnect negative battery cable.
Remove ECU cover located in right front engine compartment. If measuring unit is to be connected to fuel injection ECU, remove both fuel injection and ignition ECUs. Press adapter into ECU base. Position adapter lead at rear of ECUs and thread through slot next to ignition ECU. 2: Locating Electronic Control Units Courtesy of Volvo Cars of North America. 2) Press ignition ECU into position first to avoid damage to adapter lead.
Press fuel injection ECU, with adapter connected, into connector in bottom of ECU box. Connect measuring unit to adapter 60- pin connector. 3) If measuring unit is to be connected to ignition ECU, remove ignition ECU.
Press adapter onto ignition ECU and pull lead upward through slot beside ECU. Press ignition ECU, with adapter connected, into connector in bottom of ECU box. Connect measuring unit to adapter 60-pin connector.
3: Installing Measuring Unit & Adapter Courtesy of Volvo Cars of North America. SELF-DIAGNOSTICS Fuel Injection System Diagnostics Fuel injection ECU carries out continuous checks.
The following sensors and components supply fuel injection system ECU with information. Mass Airflow Sensor (MAF Sensor). Throttle Switch. Engine Temperature Sensor. Heated Oxygen Sensor (HO2S). A/C Compressor. Speedometer.
Automatic Transmission ECU. Ignition ECU, With Signals Indicating: Engine Speed And Cooling Fan Ignition System Diagnostics Ignition system ECU carries out continuous checks. The following sensors and components supply ignition system ECU with information.
Injectors. Idle Air Control (IAC) Valve. Fuel Pump. Main Fuel System Relay. HO2S Heating.
Emission Warning Light ENTERING SELF-DIAGNOSTICS – FUEL INJECTION SYSTEM NOTE: To perform diagnosis, turn ignition on. Ensure function selector cable is in diagnostic unit “A”, socket No.
Diagnostic Test Mode No. 1 (On-Board Diagnosis) Press test button one time quickly on diagnostic unit “A” to display codes. ECU can store 3 faults at a time in diagnostic test mode No.
Diagnostic trouble codes are stored when a faulty signal is detected. Diagnostic Test Mode No. 2 (Function Testing) Press test button 2 times to activate test mode No. LED should flash rapidly. ECU should deliver an acknowledgment code when a signal is received from the following:. 3-3-2 – Throttle switch (when throttle leaves idling position).
3-3-3 – Throttle switch (when throttle leaves full-load position). 1-1-4 – Ignition system ECU (when cooling fan is running).
1-3-4 – Low-pressure switch (when A/C compressor starts). 1-2-4 – AW50-42 A/T ECU (when gear selector lever is moved to or from a drive position.
3-3-1 – Ignition system ECU (when transmitting speed signals). Diagnostic Test Mode No.
3 (Control Testing) Press test button 3 times to activate test mode No. ECU responds by activating components in following order:. Injectors at 12 Hz for 10 seconds (5-second pause). IAC valve at one Hz for 10 seconds (5-second pause). This sequence is repeated 3 times. ENTERING SELF-DIAGNOSTICS – IGNITION SYSTEM NOTE: To perform diagnosis, turn ignition on.
Ensure function selector cable is in diagnostic unit “A”, socket No. Diagnostic Test Mode No.
1 (On-Board Diagnosis) Press test button one time quickly on diagnostic unit “A” to display codes. ECU can record and store 13 faults at a ti me in diagnostic test mode No. Diagnostic trouble codes are stored when a faulty signal is detected. Diagnostic Test Mode No. 2 (Function Testing) Press test button 2 times to activate test mode No. LED should flash rapidly. ECU should deliver an acknowledgment code when a signal is received from the following:.
1-4-1 – VSS (as flywheel rotates). 3-4-2 – CMP (as camshaft rotates). 3-4-3 – Speedometer (as front wheels rotate). 3-4-4 – Fuel injection ECU (when throttle switch is operated by opening throttle). Diagnostic Test Mode No. 3 (Control Testing) Press test button 3 times to activate test mode No.
ECU responds by activating components in following order:. Cooling fan at half speed for 15 seconds.
Cooling fan at full speed for 15 seconds (15-second pause). Variable-flow intake manifold solenoid valve for 2 Hz for 5 seconds (5-second pause). Speedometer for 5 seconds by generating a speed signal for approximately 1500 RPM (5-second pause). The sequence is repeated 3 times. DIAGNOSTIC TROUBLE CODE TESTING FUEL INJECTION DIAGNOSIS This section will cover codes dealing with fuel injection ECU testing. Codes are followed by an explanation of how to test and repair affected circuit. 1-1-2 (Fuel Injection ECU Fault) Turn ignition off.
See CLEARING CODES under SELF- DIAGNOSTIC SYSTEM. Turn ignition on and off 3-4 times. Check for code. If code is still present, replace fuel injection ECU. If code is not present, system is okay. 2-1-2 (HO2S Signal Absent Or Faulty) 1) To check HO2S sensor preheat resistor, go to step 5).
To check HO2S sensor signal, go to step 7). To check voltage supply to HO2S sensor heating element, go to next step. 2) Connect measuring unit to fuel injection ECU. See MEASURING UNIT under SELF-DIAGNOSTIC SYSTEM. Turn ignition on.
Connect voltmeter between measuring unit terminals No. If battery voltage is not present, go to next step.
If battery voltage is present, system is okay. 3) Locate oxygen sensor 2-pin connector on firewall. Use a voltmeter to backprobe between HO2S connector terminal No. 1 and ground. If battery voltage is not present, check wiring. 4: Identifying HO2S Preheater Connector Terminals Courtesy of Volvo Cars of North America. 4) If battery voltage is present, connect voltmeter between measuring unit terminals No.
Start engine. Voltage should fall from battery voltage to approximately.4 volt.
Turn engine off. If voltage reading does not fall to.4 volt, repeat test using a known good ECU. 5) Turn ignition off. To check HO2S sensor preheat resistor, connect ohmmeter between measuring unit terminals No. Depending on resistor temperature, 3-13 ohms should be present.
If 3- 13 ohms are not present, use an ohmmeter and backprobe between terminals No. 1 and 2 in HO2S 2-pin connector on firewall. 6) If approximately 3-13 ohms are present, check wire between fuel injection ECU and HO2S sensor for an open or short circuit. If sensor reading is still incorrect, replace HO2S sensor. 7) To check HO2S sensor signal, start engine.
Connect voltmeter between measuring unit terminals No. Voltage should vary between.1.9 volt after about 30 seconds.
If reading does not oscillate and voltage remains constant at.5 volt, HO2S sensor, wiring, or connector is faulty. 8) To check HO2S sensor signal at firewall connector, disconnect HO2S connector at firewall. Backprobe with voltmeter between connector terminal No. 2 and ground.
If voltage reading oscillates, check wiring between fuel injection ECU and HO2S sensor for an open or short circuit. If voltage reading remains constant at.
5 volt, repeat test using new HO2S sensor. 1-1-3 (HO2S Integrator At Maximum Enrichment Limit), 2-2-1 (Adaptive HO2S Control Rich At Part Load), 2-3-1 (Adaptive HO2S Control Lean At Part Load) & 5-1-2 (HO2S Integrator At Maximum Lean Running Limit) 1) Code 1-1-3 or 2-2-1 means that engine is running lean. This may be caused by an air leak or an HO2S sensor fault.
Code 2-3-1 or 5-1-2 means that engine is running rich. This may be caused by high fuel pressure, leaking injector(s), faulty MAF signal or faulty HO2S sensor.
2) Connect measuring unit to fuel injection ECU. See MEASURING UNIT under SELF-DIAGNOSTIC SYSTEM. To check HO2S sensor signal, start engine.
Connect voltmeter between measuring unit terminals No. Voltage should vary between.1.9 volt after about 30 seconds. 3) If voltmeter indicates a constant one or zero volts, HO2S sensor is interpreting lean air/fuel ratio or is shorted to ground. Disconnect HO2S sensor connector at firewall. Use a voltmeter and backprobe between connector terminal No.
2 and ground. 4) If voltage remains constant at zero or one volt, check engine CO adjustment. If voltage varies between.1.9 volt and code is still present, HO2S control is adjusting CO correctly but fuel injection ECU is indicating fault.
Check engine CO. 5) To check CO, connect CO meter to CO tap in exhaust pipe. Start and run engine to operating temperature. Disconnect HO2S connector. Display, record, then erase codes. 6) If meter indicates low CO and engine operates very unevenly, engine is running lean. See Codes 1-1-3 and 2-2-1.
If meter indicates high CO (greater than 2.5 percent), engine is running rich and system must make mixture leaner to compensate for fuel leakage or other fault. See Codes 2-3-1 and 5-1-2. 7) If CO content is.3-2.5 percent and engine runs normally, reconnect HO2S sensor and recheck CO content. If reading becomes too high or low, repeat test using new HO2S sensor. If CO content is still incorrect, repeat test using new fuel injection ECU. 1-2-1 (MAF Signal Absent Or Faulty) 1) Connect measuring unit to fuel injection ECU.
See MEASURING UNIT under SELF-DIAGNOSTIC SYSTEM. To check Mass Airflow (MAF) sensor signal, turn ignition on. Connect voltmeter between measuring unit terminals No.
About 2.7 volts should be present. Start engine. About 3.5 volts should be present at idle with engine hot. Turn engine off. If voltages are okay, go to step 3) and check MAF sensor ground circuit.
If voltages are not okay, go to next step. 2) Turn ignition on. Connect voltmeter between MAF sensor connector terminal No. 4 and ground.
Voltage should be about 2.7 volts. Start engine. Voltage should be about 3.5 volts during idle with engine hot. If voltages are correct, check voltage supply for an open or short circuit. If voltages are incorrect, go to next step and check MAF sensor ground circuit.
5: Identifying MAF Sensor Connector Terminals Courtesy of Volvo Cars of North America. 3) Turn ignition off. Connect ohmmeter between MAF connector terminal No. 2 and ground, then between connector terminal No.
1 and ground. Ohmmeter should indicate about zero ohms in both instances. If reading is okay, go to step 5). If reading is incorrect, go to next step. 4) Ensure ignition is off.
Connect ohmmeter between measuring unit terminals No. 20 and 8, then between terminals No. Ohmmeter should indicate about zero ohms in both instances. If reading is incorrect, repeat test using new fuel injection ECU.
If reading is correct, go to next step and check MAF sensor voltage supply. 5) Turn ignition on. Connect voltmeter between ground and MAF sensor connector terminal No. Voltmeter should indicate battery voltage.
If voltage is not present, check for an open or short circuit in voltage supply. If voltage is present, repeat test using new MAF sensor. 1-2-3 (Engine Temperature Sensor Signal Absent Or Faulty) 1) Connect measuring unit to fuel injection ECU. See MEASURING UNIT under SELF-DIAGNOSTIC SYSTEM.
Turn ignition on. Connect voltmeter between measuring unit terminals No. Voltmeter should indicate about 1.8 volts at 68 F (20 C) and about 250 millivolts when engine is at operating temperature. 2) If voltage is not to specification, check output voltage from fuel injection ECU. Disconnect temperature sensor connector.
Turn ignition on. Connect voltmeter between measuring unit terminals No. About 5 volts should be present.
3) If voltage is not to specification, check circuit between temperature sensor and ECU for an open or short circuit. If circuit is okay, repeat test using new ECU. If circuit is not okay, go to next step. 4) Ensure ignition is off. Repair circuit between temperature sensor and ECU, ensuring sensor terminal No. 14 is grounded. Connect ohmmeter between measuring unit terminals No.
Ohmmeter should indicate about zero ohms. If resistance is not to specification, repeat test using new fuel injection ECU. 5) If resistance is to specification, check resistance between measuring unit terminals No. See TEMPERATURE SENSOR RESISTANCE SPECIFICATIONS table. If resistances are not to specification, replace sensor or repair wiring as necessary.
Clear any codes in other systems. TEMPERATURE SENSOR RESISTANCE SPECIFICATIONS TABLE Temperature F ( C) Ohms 68 (20) 2800 140 (60) 560 194 (90) 206 2-2-3 (IAC Valve Signal Absent Or Faulty) 1) Check operation of idle valve in test mode No. See DIAGNOSTIC TEST MODE NO. 3 under SELF-DIAGNOSTICS.
If valve does not operate, turn ignition on. Connect voltmeter between valve connector terminal No.
2 (Green wire) and ground. If battery voltage is not present, check wiring. If battery voltage is present, check voltage between connector terminals No.
1 (Blue/Black wire) and No. 3 (Blue/White wire). If voltage is not present, check wiring. 2) Connect voltmeter between ground and connector terminal No. 1 (Blue/Black wire).
About 11 volts should be present. Connect voltmeter between ground and connector terminal No.
3 (Blue/White wire). About 5 volts should be present. If voltages are not as indicated, check wiring for an open or short circuit. If wiring is okay, replace Idle Air Control (IAC) valve. If voltages are correct or valve operates, fault may be intermittent.
Check IAC valve signal. 3) To check IAC valve signal, connect measuring unit to fuel injection ECU. Start engine. Connect voltmeter between measuring unit terminals No. About 11.8 volts should be present with engine idling at operating temperature.
Connect voltmeter between measuring unit terminals No. About 7 volts should be present. If voltage is not present as specified, check wiring. 4) To check voltage from IAC valve to fuel injection ECU, turn ignition on.
Connect voltmeter between measuring unit terminals No. About 11 volts should be present.
Connect voltmeter between measuring unit terminals No. About 5 volts should be present. Turn ignition off. 5) If no voltage was present, check wiring between valve and ECU for an open circuit.
If voltage was present, go to next step and check IAC valve coil resistance. 6) Turn ignition off. Connect ohmmeter between measuring unit terminals No. About 25 ohms should be present.
If resistance at measuring unit is incorrect, check resistance at valve connector to determine if fault is in valve or wiring. Replace valve or repair wiring as necessary.
2-3-2 (Adaptive HO2S Control Provides Richer Mixture At Idle) 1) If Codes 2-1-2 or 1-1-3 are displayed, go to step 8) and check HO2S sensor lead. If Code 2-2-1 is displayed, go to next step. 2) Disconnect Mass Airflow (MAF) sensor connector.
Turn ignition on. Connect voltmeter between MAF sensor connector terminal No. 4 and ground. If voltmeter indicates about 2.7 volts, go to next step. If voltmeter does not indicate about 2.7 volts, clean MAF sensor connector and measure voltage again. If voltage is still incorrect, repeat test using new MAF sensor. See CLEARING CODES.
3) Disconnect HO2S female connector to ECU. Turn ignition on.
Connect voltmeter between connector terminal No. 2 and ground. If about zero volts are present, check circuit between HO2S connector terminal No. 2 and fuel injection ECU for an open circuit. If voltmeter indicates more than 5 volts, check circuit between HO2S connector terminal No. 2 and fuel injection ECU for a short to voltage.
If voltmeter indicates about 2 volts, go to next step. 4) Turn ignition on. Connect voltmeter between HO2S connector terminal No. 1 and ground. If battery voltage is present, go to next step. If battery voltage is not present, check circuit between HO2S connector No.
1 and main relay No. 6: Identifying HO2S & EGR Temperature Sensor Connector Terminals Courtesy of Volvo Cars of North America. 7: Identifying Main Relay Connector Terminals Courtesy of Volvo Cars of North America. 5) Turn ignition off.
Connect an ohmmeter between both male pins of HO2S connector. If ohmmeter indicates about 3-13 ohms, (depending on temperature), go to next step. If ohmmeter does not indicate about 3-13 ohms, retest system using a new oxygen sensor. 6) Check for leakage at vacuum lines and connections. See the M – VACUUM DIAGRAMS article. If vacuum leaks are found, repair as necessary and clear codes.
If vacuum leakage is not found, go to next step. 7) Check fuel pressure. See procedures under FUEL SYSTEM in the F – BASIC TESTING article. If fuel pressure is correct, see test procedures under ELECTRONIC CONTROL UNIT – FUEL INJECTION in the I – SYSTEM/COMPONENT TESTS article. If fuel pressure is incorrect, repair as necessary. Clear codes, if present. 8) If Codes 2-1-2 or 1-1-3 were displayed in step 1), turn ignition on.
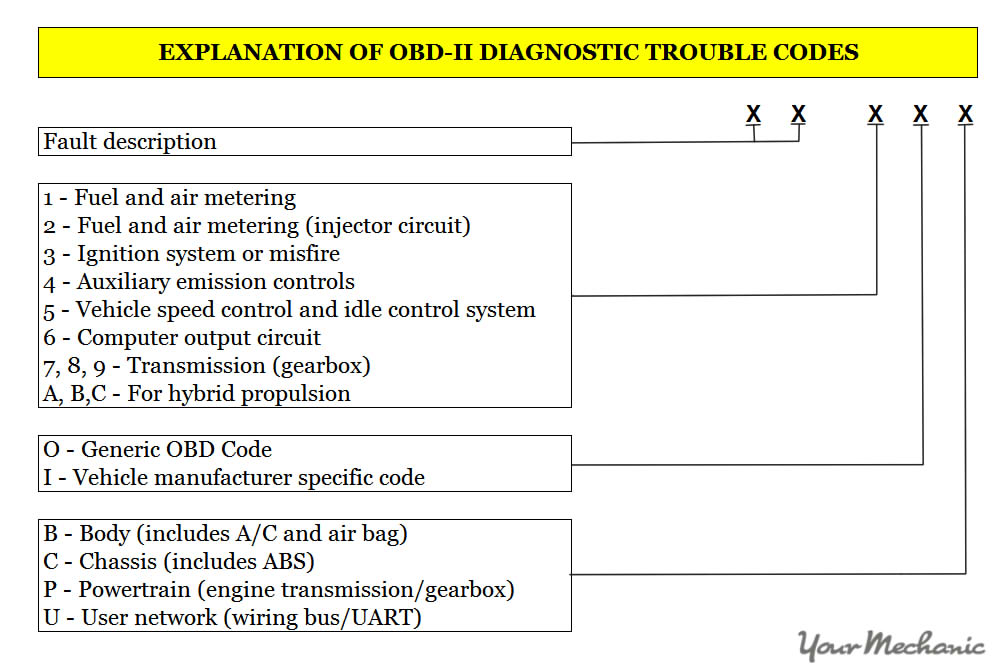
Disconnect HO2S male connector at ECU. Connect voltmeter between connector terminals No. Voltmeter should indicate approximately.4.5 volt. If voltage is to specification, go to next step.
If voltage is not to specification, reconnect connector and go to step 10). 9) Reconnect HO2S connector. Start engine and run to normal operating temperature. Connect voltmeter between HO2S connectors No. Voltmeter should indicate.1.9 volt. If voltage is not present, repeat test using new HO2S sensor.
If voltage is present, fault is intermittent. Check HO2S connector for damage or poor connection. 10) If voltage was not to specification in step 8), turn ignition off.
Disconnect fuel injection ECU. Connect an ohmmeter between connector terminals No. If ohmmeter indicates infinite resistance, check Green/Black wire between connector terminal No. 2 and ECU pin No. 22 for an open circuit.
If ohmmeter does not indicate infinite resistance, check Green/Black wire between connector terminal No. 2 and ECU pin No. 22 for a short to ground. 4-1-1 (Throttle Switch Signal Absent Or Faulty) 1) Activate diagnostic test mode No.
See DIAGNOSTIC TEST MODE NO. 2 under SELF-DIAGNOSTICS. Turn throttle slightly. If Code 3- 3-2 is displayed, switch function is okay in idling position.
2) Turn throttle to WOT and release. If Code 3-3-3 is displayed, switch function is okay in wide open position. If codes are not displayed, check throttle switch wiring, supply and resistance. If codes are displayed, fault may be intermittent. Check signal, supply and ground. 3) Connect measuring unit to fuel injection ECU. SEE MEASURING UNIT under SELF-DIAGNOSTIC SYSTEM.
Turn ignition on. Connect voltmeter between measuring unit terminals No. At idle position, about.6 volt should be present. In full load position, about 4.2 volts should be present. If voltage is not present or to specification, connect voltmeter between measuring unit terminals No. Voltmeter should indicate 5 volts.
4) Turn ignition off. Connect ohmmeter between measuring unit terminals No. Ohmmeter should indicate about zero ohms. If voltage was not present or ground connection was faulty, check wiring for short to ground or voltage.
If wiring is okay, repeat test using new fuel injection ECU. If voltage is present and resistance check shows ground is okay, go to next step. 5) Check throttle switch resistance by connecting ohmmeter between measuring unit terminals No. About 1800-2200 ohms should be present. Measure resistance between measuring unit terminals No. Resistance should be about 1000 ohms at idle and 2600 ohms at full load.
6) If resistances are not to specification, take resistance measurements at throttle switch connector to determine whether fault is in switch or wiring. If switch is faulty, replace switch.
Clear codes if any exist in other systems. Check diagnostic test mode No. 1 to check for codes in A/T and ignition system if code is displayed.
See DIAGNOSTIC TEST MODE NO. 1 under SELF-DIAGNOSTICS.
1-3-2 (Battery Voltage Too Low Or High) Connect measuring unit to fuel injection ECU. See MEASURING UNIT under SELF-DIAGNOSTIC SYSTEM. Connect voltmeter between measuring unit terminals No. Start engine and check voltmeter for battery voltage. If voltage is too low or high, check battery and charging system for malfunction. 1-3-1 (Ignition Speed System Signal Absent Or Faulty) 1) Activate test mode No.
See TEST MODE NO. 2 under SELF-DIAGNOSTICS. Operate starter motor. Code 3-3-1 should display. If code is not present, check speed signal from ignition system. If code is present, fault may be intermittent.
2) Turn ignition off. Connect measuring unit to fuel injection ECU.
See MEASURING UNIT under SELF-DIAGNOSTIC SYSTEM. Connect voltmeter between measuring unit terminals No. Operate starter motor. Voltmeter should indicate 5-7 volts. If voltage is not as specified, check wiring between fuel injection and ignition ECUs. In addition, check output signal from ignition ECU. 3) Turn ignition off.
Connect measuring unit to ignition ECU. Connect voltmeter between measuring unit terminals No. Operate starter motor. Voltmeter should indicate 5-7 volts. If voltage is not as specified, remove fuel injection ECU and repeat test. If voltage is still not present, repeat test with new ignition ECU.
3-1-1 (Speedometer Signal Absent Or Faulty) 1) Test drive vehicle. If speedometer does not operate, fault is not in fuel system. If speedometer operates during test drive, instrument cluster is receiving input signal. Activate diagnostic test mode No. 1 for instrument panel (socket No.
7) and ignition system (socket No. Display codes (if present). 2) If speedometer signal is absent and Codes 1-3-1 (instrument cluster) and 3-1-1 (ignition system) are present, wiring between instrument cluster, cruise control, and fuel injection and ignition systems is possibly open or shorted to ground or voltage. 3) To check speed signal, connect measuring unit to fuel injection ECU. See MEASURING UNIT under SELF-DIAGNOSTIC SYSTEM. Raise and support vehicle so front wheels are off ground.
Turn ignition on. Connect voltmeter between measuring unit terminals No. Spin front wheels. Voltage should vary between 0-12 volts.
If voltage is consistently high or low, check wiring for an open or short circuit. If no fault is present, replace fuel injection ECU. 5-1-1 (Adaptive HO2S Control Provides Leaner Mixture At Idle) 1) Turn ignition on. Connect voltmeter between Mass Airflow (MAF) sensor connector terminal No.
4 and ground. If voltmeter indicates about 2.7 volts, go to next step.
If voltage is not to specification, clean MAF sensor connector and repeat test. If still incorrect, repeat test using new MAF sensor.
2) Check engine oil level and condition and adjust as necessary. If oil level was incorrect or oil was contaminated, clear codes.
If oil level and oil condition are okay, check Fuel Evaporative (EVAP) system and repair as necessary. See I – SYSTEM/COMPONENT TESTS article. If EVAP system is okay, check fuel pressure. See FUEL SYSTEM in the C – SPECIFICATIONS article.
If fuel pressure is incorrect, repair as necessary and clear codes. 3) If fuel pressure is correct, check fuel injection ECU signals. See ELECTRONIC CONTROL UNIT – FUEL INJECTION in the I – SYSTEM/COMPONENT TESTS article.
IGNITION SYSTEM DIAGNOSIS 1-1-2 (ECU Fault) Clear code. Turn ignition on, wait a few seconds, then start engine. Repeat this procedure several times. If code resets, replace ignition ECU. If code does not reset, check knock control circuit by driving vehicle at high load and speed above 3000 RPM. If code returns, replace ignition ECU.
1-2-3 (Engine Temperature Sensor Signal Absent Or Faulty) 1) Activate diagnostic test mode No. 1 and check if codes have been set by fuel injection (socket No. 2) and instrument panel (socket No. See DIAGNOSTIC TEST MODE NO.
1 under SELF-DIAGNOSTICS. If fuel injection Code 1-2-3 and instrument panel Codes 1-2-1 and 1-2-2 are displayed, check fuel injection Code 1-2-3. 2) If code is present in ignition system and instrument panel but not in fuel injection system, go to next step. If code is not recorded in fuel injection system or instrument panel, go to step 4). 3) Check for an open or short circuit between fuel injection and ignition system terminals No. 53 (Green/Gray wire).
If wire is okay, repeat test using new fuel injection ECU. 4) If code is present in ignition system but not in fuel injection or instrument panel system, check wire between fuel injection and ignition system terminals No. 53 (Green/Gray wire) for an open circuit. If circuit is okay, repeat diagnosis using new ignition ECU. 1-3-1 (VSS Signal Absent) & 2-1-4 (VSS Signal Intermittent) 1) Connect measuring unit to ignition ECU.
See MEASURING UNIT under SELF-DIAGNOSTIC SYSTEM. To check VSS signal, connect voltmeter between measuring unit terminals No.
Operate starter motor. Voltmeter should indicate 300-400 millivolts with ignition switch in START position and about one volt with engine running. 2) If voltage is not present, turn ignition off. Connect an ohmmeter between measuring unit terminals No.
Resistance should be 200-400 ohms, depending on temperature. Connect ohmmeter between measuring unit terminals No.
About zero ohms should be present. 3) Disconnect Camshaft Position (CMP) sensor connector to prevent it from setting code. Use diagnostic test mode No.
2 and recheck sensor signal. See DIAGNOSTIC TEST MODE NO. 2 under SELF-DIAGNOSTICS. Operate starter motor. Code 1-4-1 should be displayed (vehicle speed sensor). If code is not displayed, repeat test using new ignition ECU.
4) If no electrical fault is found, ensure carrier plate is not damaged or distorted. This problem, which applies primarily to A/T vehicles, can prevent engine from starting and set a code. 1-4-3 (Front Knock Sensor Signal Absent Or Faulty) & 4-3-3 (Rear Knock Sensor Signal Absent Or Faulty) Connect jumper wire between knock sensor connector terminals. Connect measuring unit to ignition ECU. See MEASURING UNIT under SELF- DIAGNOSTIC SYSTEM. Connect ohmmeter between measuring unit terminals No. 22 and 23, or 24 and 25, depending on knock sensor being checked.
About zero ohms should be present. If resistance is as specified, replace knock sensor. If resistance is not as specified, check ignition ECU wiring. 1-4-4 (Load Signal From Fuel Injection System Absent/Faulty) 1) Check for codes in other systems by activating test mode No. See DIAGNOSTIC TEST MODE NO.
1 under SELF-DIAGNOSTICS. Clear codes in ignition and fuel injection systems (if present) and test drive car.
2) If code reoccurs, connect measuring unit to ignition ECU. See MEASURING UNIT under SELF-DIAGNOSTIC SYSTEM. Start engine. Connect voltmeter between measuring unit terminals No. With engine idling at normal operating temperature, approximately 50 millivolts should be present.
Voltage reading should increase with engine RPM. If signal is present, repeat diagnostic test using different ignition ECU. 3) If signal is not present, turn ignition off. Connect ohmmeter between measuring unit terminals No. Infinite ohms should be present.
If zero ohms are present, circuit is shorted to ground. 4) Connect voltmeter between measuring unit terminals No. Turn ignition on. If battery voltage is present, circuit is shorted to voltage. 5) If voltage readings are okay but signal is still not present, measure resistance in circuit between ignition ECU terminal No. 12 and fuel injection ECU terminal No. 12 (Pink wire).
If circuit is okay but signal is still not present, repeat test using new fuel injection ECU. Clear all codes in all other systems. See DIAGNOSTIC TEST MODE NO. 1 under SELF-DIAGNOSTICS. 1-5-4 (EGR System Leakage) 1) Symptom of EGR system leakage is rough idle. Code will set when engine temperature is 150 F (65 C) or less, and temperature sensor detects an increasing temperature. If ECU detects that temperature of EGR temperature sensor varies by more than a preset limit before temperature has reached 150 F (65 C), ECU will interpret condition as an EGR flow and will initiate a code.
Some faults that can produce this code include:. Leaking EGR valve. Signal to EGR controller faulty. EGR controller defective.
Poor ground. Engine thermostat defective. 2) Start engine and listen to idle. If idle is okay, go to step 4) and check engine temperature.
If idle is not okay, disconnect EGR controller connector. If idle is still rough, go to next step and check EGR controller. If idle is now okay, check Green/Brown wire between ignition ECU terminal for a short to ground.
Volvo I Shift Fault Codes
3) To check EGR controller, run engine at idle. Carefully disconnect Yellow hose from EGR controller.
If idle is now okay, repeat test using new EGR controller. If idle is still rough, turn ignition off. Carefully disconnect Yellow hose from EGR valve. Check hose for blockage or leaks.
If Yellow hose is okay, repeat test using new EGR valve. If hose is blocked or leaking, replace hose. In both cases, clear codes.
4) Check engine temperature gauge with engine running. If gauge pointer does not rise to normal and top radiator hose is hot, go to next step. If gauge shows normal operating temperature and top radiator hose is hot, go to step 6). If gauge pointer rises slowly and top radiator hose is not at normal operating temperature, retest system using new thermostat. 5) Turn ignition off. Disconnect Mass Airflow (MAF) sensor connector. Connect an ohmmeter between MAF sensor connector terminal No.
2 and ground. If ohmmeter indicates about zero ohms, go to next step. If ohmmeter does not indicate about zero ohms, disconnect electrical connector located under intake manifold, on engine block. Clean and reconnect connector. 6) Code may be set by contact resistance at EGR and engine temperature sensor connector. Clean and protect EGR and engine temperature sensor connectors from oxidation, dirt, etc.
2-4-1 (EGR Flow Incorrect) 1) EGR temperature sensor signal should change when signal from ECU is sent to vacuum controller. If signal does not change, ECU registers a fault and sets code. Possible faults include:. Break in signal lead. No voltage at EGR controller. Faulty EGR controller. Poor vacuum supply to EGR valve (White vacuum hose).
Faulty Yellow vacuum hose. EGR valve does not open. 2) To check operation of EGR vacuum controller, start and run engine so it reaches normal operating temperature. Put hand on EGR controller and increase engine speed several times over 2000 RPM. If EGR controller produces a ticking sound, go to next step. If EGR controller is not ticking, go to step 9) and check voltage supply to EGR controller.
3) Ensure engine is still running. Carefully disconnect White vacuum hose from EGR controller and check for vacuum.
If vacuum is not present, check White vacuum hose between controller and intake manifold. If vacuum is present, go to next step and check vacuum from EGR controller. 4) Turn ignition off. Reconnect White vacuum hose to EGR controller.
Carefully disconnect Yellow vacuum hose from EGR controller. Connect vacuum gauge to EGR controller. Start engine. Increase engine speed repeatedly. If gauge pointer moves rapidly, verifying EGR controller is passing vacuum, go to step 6) and check EGR valve. If gauge does not move rapidly, go to next step. 5) Turn ignition off.
Carefully disconnect Yellow vacuum hose at both ends. Check Yellow vacuum hose for blockage. If hose is okay, repeat test using new EGR controller. If hose is blocked, repeat test using new vacuum hose. 6) To check EGR valve, turn ignition off.
Reconnect Yellow vacuum hose to EGR valve. Connect vacuum pump to Yellow vacuum hose at EGR controller.
Start engine. Increase vacuum to 9 in. Ensure EGR valve retains vacuum (engine will run rough). 7) If engine runs rough when vacuum pump shows vacuum but vacuum pump loses vacuum, check Yellow vacuum hose for leakage. If hose is okay, retest using new EGR valve.
If engine idles evenly when vacuum pump shows vacuum and vacuum pump maintains vacuum, ensure EGR pipe is not blocked. If pipe is not blocked, repeat test using new EGR valve.
8) If engine idles rough when vacuum pump shows vacuum and vacuum pump maintains vacuum, fault is intermittent. Check vacuum controller connector. If connector is okay, check Green/Brown wire between EGR controller terminal No.
1 and ignition ECU terminal No. 27 for intermittent short to voltage or ground. 9) If EGR controller was not ticking in step 2), check voltage at EGR controller.
Turn ignition on. Disconnect EGR controller connector. Connect voltmeter between EGR controller connector terminal No.
2 and ground. If voltmeter indicates battery voltage, go to next step and check signal lead. If no voltage is present, check for open circuit in Green wire between EGR controller terminal No. 2 and main relay terminal No. 8: Identifying EGR Controller Connector Terminals Courtesy of Volvo Cars of North America. 10) To check signal lead, turn ignition on.
Disconnect EGR controller connector. Connect voltmeter between wiring side of EGR controller terminals No.
If battery voltage is not present, check for open circuit or short to voltage in Green/Brown wire between EGR controller terminal No. 1 and ignition ECU terminal No.
If battery voltage is present, go to next step. 11) To check EGR controller resistance, turn ignition off. Disconnect EGR controller connector. Connect an ohmmeter between EGR controller terminals. If ohmmeter shows 75-95 ohms at 68 F (20 C), check EGR controller connections for oxidation. If ohmmeter does not show 75-95 ohms at 68 F (20 C), repeat test using new EGR controller.
3-1-1 (Speedometer Signal Absent Or Faulty) 1) Test drive vehicle. If speedometer does not operate, fault is not in ignition system.
If speedometer operates during test drive, instrument cluster is receiving input signal. Activate diagnostic test mode No. 1 for instrument cluster (socket No. 7) and fuel injection system (socket No. See DIAGNOSTIC TEST MODE NO.
1 under SELF-DIAGNOSTICS. Display codes (if present). 2) If speedometer signal is absent, and Codes 1-3-1 (instrument cluster) and 3-1-1 (fuel injection system) are present, wiring between instrument cluster, cruise control, and fuel injection and ignition systems is possibly open or shorted to ground or voltage. 3) To check speed signal, connect measuring unit to ignition ECU. See MEASURING UNIT under SELF-DIAGNOSTIC SYSTEM. Raise and support front wheels of vehicle. Turn ignition on.
Volvo Excavator Fault Codes
Connect voltmeter between measuring unit terminals No. Spin front wheels. Voltage should vary between 0-12 volts.
If voltage is consistently high or low, check wiring for an open or short circuit. If no fault is present, replace ignition ECU. 3-1-4 & 3-2-4 (Camshaft Position Sensor Signal Absent/Faulty) 1) Turn ignition off.
Connect measuring unit to ignition ECU. See MEASURING UNIT under SELF-DIAGNOSTIC SYSTEM. Connect voltmeter between measuring unit terminals No. Operate starter motor. Voltage should vary between.1-5 volts. If voltage is incorrect, take measurement directly at Camshaft Position (CMP) sensor.
2) Turn ignition off. If signal is still absent or faulty, check CMP ground and supply by connecting an ohmmeter between measuring unit terminals No. About zero ohms should be present. If reading is incorrect, repeat test using new ignition ECU. 3) To check CMP supply voltage, connect voltmeter between measuring unit terminals No. Turn ignition on. Approximately 10 volts should be present.
If voltage supply and ground connections are okay, but signal is still not present, take measurement at CMP connector. If voltage supply and ground connections are okay, but signal is still not present, replace CMP.
4) To check CMP signal in diagnostic test mode No. 2, disconnect Vehicle Speed Sensor (VSS) connector to prevent it from displaying a trouble code. Activate diagnostic test mode No. See DIAGNOSTIC TEST MODE NO.
2 under SELF-DIAGNOSTICS. Start engine. Code 3-4-2 should be displayed. If code is not displayed, repeat test using new ignition ECU. 4-1-1 (Throttle Switch Signal Absent Or Faulty) 1) Activate fuel injection diagnostic test mode No.
See DIAGNOSTIC TEST MODE NO. 1 under SELF-DIAGNOSTICS. Check whether throttle switch code recorded. If code recorded, see 4-1-1 (THROTTLE SWITCH SIGNAL ABSENT OR FAULTY) under FUEL INJECTION DIAGNOSIS. If fault is not in fuel injection system, connect measuring unit to ignition ECU. See MEASURING UNIT under SELF-DIAGNOSTIC SYSTEM.
2) Ensure ignition is off. Connect ohmmeter between measuring unit terminals No. Very high or infinite resistance should be present. A reading of zero ohms indicates a short to ground is present. 3) Connect voltmeter between measuring unit terminals No. Turn ignition on.
If battery voltage is present, circuit is shorted to voltage. If resistance and voltage measurements are okay but signal is still absent, turn ignition off. 4) Use an ohmmeter and check continuity between ignition and fuel injection ECU terminals No. 20 (Green/Brown wire). If circuit is okay but signal is still not present, repeat test using a known good fuel injection ECU. Clear codes if any exist in other systems. Check diagnostic test mode No.
1 to check for codes in A/T and ignition system if code is displayed. See DIAGNOSTIC TEST MODE NO. 1 under SELF-DIAGNOSTICS.
4-1-3 (EGR Temperature Sensor Signal Incorrect/Missing) 1) ECU uses EGR temperature sensor signal to determine whether an EGR flow is present. A code will set if signal from sensor to ECU is too high, too low or incorrect. Following fault sources can cause an incorrect or missing EGR temperature sensor:. Faulty EGR temperature sensor (open or short circuit). Signal lead short circuit. Signal lead short circuit to ground.
Ground lead open circuit. Signal lead short circuit to another lead. Loose contact at EGR temperature sensor connector. Tracking current at EGR temperature sensor connector. 2) Turn ignition off.
Disconnect EGR temperature sensor. Check and clean EGR temperature sensor connector. Connect ohmmeter between wiring side of temperature sensor connector terminal No. 2 and ground. 3) If ohmmeter indicates about zero ohms, go to next step and check signal lead.
If ohmmeter shows infinite resistance, check Green/Black wire between temperature sensor connector terminal No. 2 and ignition ECU terminal No. 16 for an open circuit. If ohmmeter shows more than 5 ohms, disconnect ground wire located under intake manifold on engine block. Clean and reconnect connector. 4) To check signal lead, turn ignition on. Disconnect EGR temperature sensor connector.
Connect voltmeter between EGR temperature sensor terminals No. If voltmeter indicates about 5 volts, go to step 6) and check EGR temperature sensor. If voltmeter indicates about zero volts, go to step 9) and check signal lead resistance. 5) If voltmeter shows more than 5 volts, check Green/Yellow wire between EGR temperature sensor terminal No. 1 and ignition ECU terminal No.
5 for short to voltage. In addition, EGR temperature sensor can be faulty if signal lead has shorted to voltage. For this testing, go to next step.
6) To check EGR temperature sensor, turn ignition off. Reconnect EGR temperature sensor connector. Connect measuring unit to ignition ECU. See MEASURING UNIT under SELF-DIAGNOSTIC SYSTEM.
Disconnect ignition ECU. Connect ohmmeter between measuring unit terminals No. If ohmmeter indicates about 2000 ohms at 68 F (20 C), go to next step. If infinite resistance is present, repeat test using new EGR temperature sensor. 7) To check EGR temperature sensor signal, reconnect ignition ECU and start engine.
Connect voltmeter between measuring unit terminals No. Voltmeter should indicate 1.8-4.6 volts depending on temperature (voltage drops as temperature rises). 8) Disconnect Yellow vacuum line from EGR controller.
Connect vacuum pump to hose facing EGR valve. Increase vacuum.
Engine should idle rough. If voltage drops slowly as temperature rises, temperature sensor is okay. Check EGR temperature sensor connector for poor connection. If voltage does not drop as temperature rises, retest using new EGR temperature sensor. 9) If voltmeter indicated about zero volts in step 4), check resistance of signal lead to ground. Turn ignition off.
Disconnect ignition ECU. Connect ohmmeter between EGR temperature sensor terminals No.
If ohmmeter indicates infinite resistance, check Green/Yellow wire between EGR temperature sensor terminal No. 1 and ignition ECU terminal No.
5 for an open circuit. If ohmmeter does not indicate infinite resistance, check Green/Yellow wire for a short to ground. In both instances, clear codes. 4-3-2 & 5-1-3 (High Temperature Warning In ECU Box) Code 4-3-2 is recorded if temperature in ECU box exceeds 185 F (85 C) for more than 18 seconds.
Code 5-1-3 is recorded if temperature continues to rise and exceeds 203 F (95 C) for more than 18 seconds. If this problem is persistent, install accessory fan kit in ECU holder. SUMMARY If no hard fault codes (or only pass codes) are present, driveability symptoms exist or intermittent codes exist, proceed to the H – TESTS W/O CODES article for diagnosis by symptom (i.e., ROUGH IDLE, NO START, etc.) or intermittent diagnostic procedures. Disclaimer: Volvotips has the exclusive courtesy of Volvo Car Corporation and Volvo Cars Heritage to publish the Volvo Greenbooks (service manual), parts catalogs and other Volvo-material and publications.
Commercial use and publishing at other websites of these items is prohibited.
Volvo excavator fault code table SAE- code, converted into a fault code (with D12C engine) Machine serial number EC330B 10236 EC360B 10829 Maintenance tools VCADS Pro using SAE type of fault codes. SAE fault code design including, for example MID, PID and FMI following identification numbers. MID: Message Identification Description (a control component identification). Each control unit has a unique number.
PID: Parameter Identification D escription (indicated parameters / identification values). Each parameter has a unique number. PPID: Proprietary Parameter I dentification Description (expressed Volvo unique parameter values / identification). Each parameter has a Volvo unique number.
SID: Subsystem Identification D escription (indicated component recognition). SID number is determined by which they transfer control assembly (MID) from coming. Each control module has its own SID number sequence. The exception is SID numbers 151-255, which are common to all systems.
PSID: Proprietary Subsystem I dentification Description. (Expressed Volvo unique component recognition).
FMI: Failure Mode I dentifier (represented identify the fault type). Troubleshooting information is based on Volvo (Volvo) excavator fault code. When reading a fault code on the VCADS Pro, for further troubleshooting, SAE fault code must be converted to Volvo excavator fault code. The following is the fault codes to Volvo excavator SAE fault code conversion tables.