Hino Manual
Some HINO Truck Operator Manuals PDF shown above. HINO Automobile concern at the moment is one of the largest Japanese automotive factories for the production of medium and large truck tonnage. Thread automobile plant history stretches from the first truck manufacturers - Japan: Tokyo shipyard « Tokyo Ishikawajima Shipbuilding - Engineering Co» and Tokyo Gas and Electric Company - « Tokyo Gas Electric Industry Co». These companies produce almost identical trucks wore the brand « Sumida» and « Chiyoda». And in 1937 when the company merged with each other, produced trucks got another name (Service Manuals PDF page).
But in 1941 after another company regrouping their forces once again changes its name to « Diesel Motor Industry Co». A little later, in 1942, again there was a reconstruction in which the enterprise which owned the company TGE, separated and at the same time took the name « Hino Heavy Industry Co». In the department of the company continued to work on the production of a 7-ton truck with a 6-cylinder diesel engines air cooling capacity of which was 125 hp In 1996, the company « HINO» released its 2-millionth car. In Japan, it owns 8 plants with about 10 thousand personnel, including the largest robotic complex in Hamura near Tokyo, which made all the assemblies and parts for cars. In addition, the company has several assembly plants in the US, Ireland, Thailand, Egypt, Malaysia, the Philippines.
By the end of the XX century they produced annually by 80-90 thousand. Lorries and buses, including trucks with full weight more than 6 m.
Approximately 33 thousand pieces. In terms of production the company occupies 16 th place in the world and third in Japan. HINO Trucks are available in more than 100 countries worldwide. But not so long ago, the concern decided to try his truck on the Dakar.
Hino 500 Series Factory Service Workshop Manual download on PDF can be viewed using free PDF reader like,. File size 216 Mb document. It is compressed as a zip file which you can extract with Engine J05D-TI, J05E-TI, J08E-TI, A09C Model: FC6J, FC9J, FD8J, GD8J, FG8J, GH8J, FL8J, FM8J, FM1A, FM2P, SG8J, FT8J, GT8J series Chassis Workshop Manuals S1-YFCE18K 1/3, S1-YFCE18K 2/3, S1-YFCE18K 3/3 Electrical Wiring Diagrams S1-YFCE18K EWD J05D-TI. J05E-TI Engine Workshop Manual S5-YJ05E12D J08E-TI Engine Workshop Manual S5-YJ08E29E A09C Engine Workshop Manual S5-MA09E02B Contents Foreword General Introduction Engine introduction Engine Mechanical Air Intake System Exhaust System Lubricating System Cooling System Fuel System Turbocharger Engine P.T.O Engine Retarder Hino 500 Series Factory Service Workshop Manual download Quantity. The diesel engine (also known as a compression-ignition engine) is an inner combustion engine that uses the heat of compression to initiate ignition and burn the fuel that happens to be injected into the combustion chamber. This contrasts with spark-ignition engines such as a petrol engine (gasoline engine) or gas engine (using a gaseous fuel as opposed to gasoline), which use a spark plug to ignite an air-fuel mixture. The diesel engine gets the greatest thermal efficiency of any standard internal or external burning engine due to its very high compression ratio.
Low-speed diesel machines (as used in ships and various other applications exactly where overall engine weight is relatively unimportant) can have a thermal efficiency that surpasses 50%. Diesel engines are manufactured in two-stroke and four-stroke versions. They were originally used as a much more efficient replacement for stationary steam engines. Because the 1910s they have been used in submarines and ships. Use in locomotives, trucks, hefty gear and electric generating plants followed later on. In the 1930s, they slowly began to be made use of in a couple of automobiles.
Since the 1970s, the use of diesel engines in larger on-road and off-road vehicles in the USA increased. According to the British Society of Motor Manufacturing and Traders, the EU average for diesel cars take into account 50% of the total sold, including 70% in France and 38% into the UK. Diesel engines have the lowest specific fuel consumption of any large internal combustion engine employing a single cycle, 0.26 lb/hp (0.16 kg/kWh) for very large marine engines (combined cycle energy flowers are much more efficient, but employ two engines rather than one).
Two-stroke diesels with large pressure forced induction, particularly turbocharging, make up a large percentage of the very largest diesel engines. In North America, diesel engines are primarily used in large trucks, where the low-stress, high-efficiency period leads to much longer engine life and lower working costs. These advantages also make the diesel engine ideal for use in the heavy-haul railroad environment.
Diesel's original engine injected fuel with the assistance of compressed air, which atomized the fuel and pushed it into the engine through a nozzle (a similar principle to an aerosol spray). The nozzle opening had been closed by a pin valve lifted by the camshaft to initiate the fuel injection before leading dead centre (TDC). This is called an air-blast injection. Driving the three stage compressor used some power but the effectiveness and net power output ended up being even more than any other combustion engine at that time.
Diesel engines in service today raise the fuel to extreme pressures by mechanical pumps and provide it towards the combustion chamber by pressure-activated injectors without compressed air. With direct injected diesels, injectors spray fuel through 4 to 12 small orifices in its nozzle. The early air injection diesels always had a superior burning without the sharp increase in pressure during combustion. Scientific studies are now being performed and patents are being taken out to again use some kind of air injection to reduce the nitrogen oxides and pollution, reverting to Diesel's original implementation with its superior combustion and possibly quieter procedure. In all major aspects, the modern diesel engine keeps true to Rudolf Diesel's original design, that of igniting fuel by compression at an incredibly high pressure within the cylinder.
With much higher pressures and high technology injectors, present-day diesel engines make use of the so-called solid injection system used by Herbert Akroyd Stuart for his hot bulb engine. The indirect injection engine could be considered the newest development of these low speed hot bulb ignition engines.
A vital component of all diesel engines is mechanical or digital governor which regulates the idling speed and maximum speed of the engine by controlling the rate of fuel delivery. Unlike Otto-cycle engines, incoming air is not throttled and a diesel engine without a governor cannot have a stable idling speed and can easily overspeed, leading to its destruction. Mechanically governed fuel injection systems are driven by the engine's gear train. These systems use a combination of springs and weights to control gas delivery relative to both load and speed. Modern electronically controlled diesel engines control fuel delivery by use of an electronic control module (ECM) or digital control unit (ECU).
The ECM/ECU receives an engine speed signal, since well as various other operating parameters such as intake manifold stress and gasoline temperature, from a sensor and controls the quantity of fuel and start of injection timing through actuators to maximise minimise and power and efficiency emissions. Controlling the timing of the beginning of injection of fuel into the cylinder is a key to minimizing emissions, and maximizing fuel economy (efficiency), of the motor. The timing is measured in degrees of crank angle of the piston before top dead centre. For instance, if the ECM/ECU initiates fuel injection when the piston is before TDC, the start of injection, or timing, is said to be BTDC. Optimal timing will rely on the engine design as well as its load and speed, and is generally BTDC in 1,350-6,000 HP, net, 'medium speed' locomotive, marine and stationary diesel engines. Advancing the start of injection (injecting prior to the piston reaches to its SOI-TDC) results in greater in-cylinder pressure and temperature, and greater efficiency, but also results in increased engine noise due to faster cylinder pressure rise and increased oxides of nitrogen (NOx) formation due to higher burning temperatures.
Delaying start of injection causes incomplete combustion, decreased fuel efficiency and an enhance in exhaust smoke, containing a considerable amount of particulate matter and unburned hydrocarbons. The term Indirect injection, in an internal burning engine, refers to fuel injection where fuel is not directly inserted into the combustion chamber. Gasoline motors are generally equipped with indirect injection systems, wherein a fuel injector delivers the fuel at some time before the intake valve. An indirect injection diesel engine delivers gasoline into a chamber off the combustion chamber, called a prechamber, where combustion begins and then spreads into the primary combustion chamber. The prechamber is carefully made to ensure sufficient blending of the atomized fuel with the compression-heated air.
The purpose of this divided combustion chamber is to speed up the combustion procedure, to be able to increase the power output by increasing engine rate. The addition of a prechamber, nevertheless, boosts heat loss to the cooling system and thereby lowers engine efficiency. The engine requires glow plugs for starting. In an indirect injection system the environment moves fast, mixing the fuel and environment. This simplifies injector design and enables the employment of smaller engines and less tightly toleranced designs which are simpler to manufacture and much more reliable.
Direct injection, by contrast, uses slow-moving atmosphere and fast-moving fuel; both the design and manufacture of the injectors is more difficult. The optimisation of the in-cylinder air flow is much more difficult than designing a prechamber. There is a great deal more integration between the design of the injector and also the engine. Information technology is for this reason that car diesel engines were nearly all indirect injection until the ready accessibility of powerful CFD simulation systems made the adoption of direct shot practical. Information technology consists of a spherical chamber located in the cylinder head and divided from the engine cylinder by a tangential throat. About 50% of the atmosphere enters the swirl chamber during the compression stroke for the engine, producing a swirl.
After combustion, the products return through the exact same throat to the main cylinder at much higher velocity. So more heat loss to walls of the passage takes place. This kind of chamber finds application in engines in which fuel control and engine stability are more important than fuel economy. These are Ricardo chambers. The air cell is a small cylindrical chamber with a hole in a single end. It is mounted more or less coaxially with the injector, said axis being parallel to the piston crown, with the injector firing across a small cavity which is available to the cylinder into the hole within the conclusion of the air cellular. The air cellular is mounted therefore as to minimise thermal contact with the mass associated with the head.
A pintle injector with a slim spray pattern is used. At TDC the vast majority of the charge mass is contained in the cavity and air cell. When the injector fires, the jet of fuel enters the air cell and ignites. This leads to a jet of flame shooting back out of the air cell directly into the jet of fuel still issuing from the injector.
The turbulence and heat give excellent gas vaporisation and blending properties. Also since the majority of the combustion requires place outside the environment cell within the cavity, which communicates directly utilizing the cylinder, there is much less temperature loss involved in transferring the burning charge to the cylinder.
Air cell injection can be looked at as a compromise between direct and indirect injection, gaining a few of the efficiency advantages of direct injection while retaining the ease and simplicity of development of indirect injection. Indirect injection is much less complicated to design and manufacture; less injector development is required and the shot challenges are low (1500 psi/100 bar versus 5000 psi/345 bar and higher for direct injection) The reduced stresses that indirect injection imposes on internal components imply that it is possible to produce petrol and indirect injection diesel variations of the same basic engine. At best such types differ only in the cylinder head and the demand to fit a distributor and spark plugs in the petrol version whilst fitting a shot pump and injectors to the diesel.
Examples are the BMC A-Series and B-Series engines together with Land Rover 2.25/2.5-litre 4-cylinder types. Such styles allow petrol and diesel versions of the same vehicle to be built with minimal design modifications between them. Higher engine speeds can be reached, since burning continues in the prechamber.
In cold weather condition, high speed diesel engines can be difficult to start because the mass of the cylinder block and cylinder head absorb the heat of compression, preventing ignition as a result of the higher surface-to-volume proportion. Pre-chambered engines make usage of small electric heaters inside the pre-chambers called glowplugs, while the direct-injected engines have these glowplugs in the combustion chamber.
Many engines use resistive heaters within the intake manifold to warm the inlet air for starting, or until the motor reaches running temperature. Engine block heaters (electric resistive heaters in the motor block) connected to the utility grid are used in cold environments whenever an engine is turned off for extended periods (more than an hour), to reduce startup engine and time wear. Block heaters are also used for emergency power standby Diesel-powered generators which must rapidly pick up load on an energy failure. In the past, a wider variety of cold-start methods were used. Some engines, such as Detroit Diesel engines used a system to present small amounts of ether into the inlet manifold to start burning.
Others used a mixed system, with a resistive heater burning methanol. An impromptu method, particularly on out-of-tune motors, is to manually spray an aerosol can of ether-based motor starter fluid into the intake air flow (usually through the intake air filter assembly). Most diesels are now turbocharged and some are both turbo charged and supercharged. Because diesels do not have fuel in the cylinder before combustion is initiated, one or more bar (100 kPa) of air can be loaded in the cylinder without preignition.
A turbocharged engine can produce significantly more energy than a naturally aspirated engine of the same configuration, as having more air in the cylinders allows more fuel to be burned and thus more power to be produced. A supercharger is powered mechanically by the engine's crankshaft, while a turbocharger is powered by the engine exhaust, not requiring any mechanical energy. Turbocharging can enhance the fuel economy of diesel engines by recovering waste heat from the exhaust, increasing the excess air factor, and increasing the ratio of engine output to friction losses. A two-stroke engine does not have a discrete exhaust and intake stroke and thus is incapable of self-aspiration. Therefore all two-stroke engines must be fitted with a blower to charge the cylinders with air and assist in dispersing exhaust gases, a procedure referred to as scavenging. Sometimes, the engine may additionally be fitted with a turbocharger, whose output is directed into the blower inlet.
A few styles employ a hybrid turbocharger (a turbo-compressor system) for scavenging and asking the cylinders, which device is mechanically driven at cranking and low speeds to act as a blower, but which will act as a true turbocharger at higher speeds and loads. A hybrid turbocharger can revert to compressor mode during instructions for large increases in engine output power.
As supercharged or turbocharged engines produce more power for a given engine dimensions as compared to naturally aspirated attention, engines must be compensated to the mechanical design of components, lubrication, and cooling to handle the power. Pistons are usually cooled with lubrication oil sprayed on the bottom of the piston. Large engines may use sea, water water, or oil supplied through telescoping pipes attached to the crosshead. As with petrol engines, there are two classes of diesel engines in current use: two-stroke and four-stroke.
The four-stroke kind is the 'classic' variation, tracing its lineage back to Rudolf Diesel's prototype. It is additionally the most frequently used form, becoming the preferred power source for many motor vehicles, especially trucks and buses. Much larger engines, such as useful for railway locomotion and marine propulsion, are often two-stroke units, offering an even more favourable power-to-weight ratio, in addition to better fuel economic climate.


The most powerful engines in the world are two-stroke diesels of mammoth dimensions. Two-stroke diesel engine procedure is similar to that of petrol counterparts, except that fuel is not mixed with air before induction, and the crankcase does not take an active role in the period. The traditional two-stroke design relies upon a mechanically driven positive displacement blower to recharge the cylinders with air before compression and ignition.
The charging process also assists in expelling (scavenging) combustion fumes continuing to be from the previous power stroke. The archetype of the modern form of the two-stroke diesel is the (high-speed) Detroit Diesel Series 71 motor, developed by Charles F. 'Boss' Kettering and his colleagues at General Motors Corporation in 1938, in which the blower pressurizes a chamber in the engine block that is usually referred to as the 'air box'. The (extremely much larger medium-speed) Electro-Motive Diesel motor is used as the prime mover in EMD diesel-electric locomotive, marine and stationary applications, and was developed by the same team, and is built to the same principle. However, a significant improvement constructed into most later EMD engines is the mechanically-assisted turbo-compressor, which provides charge air utilizing mechanical assistance during starting (thereby obviating the necessity for Roots-blown scavenging), and provides charge air using an exhaust gas-driven turbine during normal operations—thereby providing true turbocharging and additionally increasing the engine's power output by at least fifty percent.
In a two-stroke diesel engine, as the cylinder's piston approaches the bottom dead centre exhaust ports or valves are opened relieving many of the excess pressure after which a passage between the air box and the cylinder is opened, permitting air flow into the cylinder. The environment movement blows the remaining combustion gases from the cylinder—this is the scavenging process. Because the piston passes through bottom centre and starts up, the passageway is closed and compression commences, culminating in fuel injection and ignition. Refer to two-stroke diesel engines for more detailed coverage of aspiration types and supercharging of two-stroke diesel engines.
Normally, the number of cylinders are used in multiples of two, although any number of cylinders can be used as long as the load on the crankshaft is counterbalanced to prevent excessive vibration. The inline-six-cylinder design may be the many respected in light- to medium-duty engines, though small V8 and larger inline-four displacement engines are also common. Small-capacity engines (generally considered to be those below five litres in capacity) are generally four- or six-cylinder kinds, with the four-cylinder being the most common type found in automotive utilizes. Five-cylinder diesel engines have actually also already been created, becoming a compromise between the sleek running of the six-cylinder and the space-efficient dimensions of the four-cylinder. Diesel engines for smaller sized plant machinery, ships, tractors, generators and pumps may be four, three or two-cylinder types, with the single-cylinder diesel engine remaining for light stationary work.
Direct reversible two-stroke marine diesels need at least three cylinders for reliable restarting forwards and reverse, while four-stroke diesels need at least six cylinders. The need to enhance the diesel engine's power-to-weight ratio produced several novel cylinder arrangements to draw out more power from an offered ability. The uniflow opposed-piston engine uses two pistons in a single cylinder with the combustion cavity in the centre and gas in- and outlets at the ends.
This makes a comparatively powerful, light, swiftly running and economic engine suitable for use in aviation. An example is the Junkers Jumo 204/205.
The Napier Deltic engine, with three cylinders arranged in a triangular formation, each containing two opposed pistons, the whole engine having three crankshafts, is among the better known. Hino engines, Ltd. Is a Japanese manufacturer of commercial automobiles and diesel engines (like for vehicles, buses along with other motors) headquartered in Hino-shi, Tokyo. The business is a respected producer of moderate and heavy-duty diesel trucks in Asia. Hino Motors is a constituent associated with the Nikkei 225 regarding Tokyo stock market. It's a subsidiary of Toyota engine organization and another of 16 significant organizations associated with the Toyota team.
The company traces its roots back to the founding of Tokyo petrol markets team in 1910. In 1910 Chiyoda Gas Co.
Had been established and competed fiercely against incumbent Tokyo Gas Company combat for gasoline lighting users. Tokyo Gas markets had been a parts supplier for Chiyoda gasoline but it ended up being beaten and merged into Tokyo fuel in 1912.
Dropping their largest customer, Tokyo petrol business Co. Broadened their products like digital parts, and renamed itself as Tokyo fuel and electricity Industry, TG&E and is frequently abbreviated as Gasuden. They produced their first motor vehicle in 1917, the design TGE 'A-Type' vehicle. In 1937, TG&E joined their car division with that of Automobile markets Co., Ltd. And Kyodo Kokusan K.K., to form Tokyo vehicle business Co., Ltd., with TG&E as a shareholder.
Four ages later on, the organization changed their title to Diesel engine Industry Co., Ltd., which would sooner or later become Isuzu engines restricted. Listed here season (1942), the newest entity of Hino significant business Co., Ltd. Spun it self from Diesel engine markets Co., Ltd., and the Hino title was born. During globe War II, Hino manufactured Type 1 Ho-Ha half-track and Type 1 Ho-Ki armored employees service for the Imperial Japanese Army.
Following end of globe War II, the organization must stop producing huge diesel machines for aquatic solutions, and with the signing of pact, the company fallen the 'hefty' from the title and formally focused from the heavy-duty trailer-trucks, buses and diesel machines areas, as Hino markets Co., Ltd. The business took its title through the area of the head office in Hino town within Tokyo prefecture.
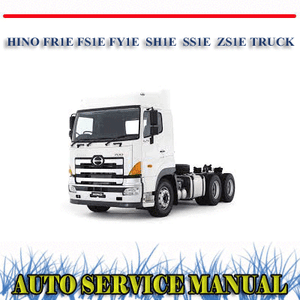
To sharpen its advertisements focus to customers, in 1948, the business included the name 'Diesel' to be Hino Diesel markets Co., Ltd. In 1950 the heavy-duty TH10 had been launched, equipped with the all-new 7-liter DS10 diesel system. An eight-tonner, this is significantly bigger than current Japanese vehicles which have rarely already been built for significantly more than 6,000 kg (13,230 pound) payload.
In 1953, Hino registered the private automobile marketplace, by production Renaults under licence, as well as in 1961 it going building a unique Contessa 900 sedan with an 893cc rear-mounted motor, and a pickup truck known as the Hino Briska because of the Contessa system a little enlarged and setup right in front with back wheel drive. The Italian stylist Giovanni Michelotti redesigned the Contessa range in 1964 with a 1300 cc rear-mounted system. Fed by two SU type carburettors, this developed 60 hp (44 kW) into the sedan and 70 hp (51 kW) in the coup variation. But Hino ceased personal car manufacturing quickly in 1967 after joining the Toyota team.
In 1963, the Hamura factory began procedures, and focused on commercial vehicle and coach manufacture. Hino Trucks are also assembled in Portugal as well as in Canada. Hino Motors signed a 10-year assembly agreement with Kaiser-Illin companies of Haifa, Israel, in 1963. System of Contessa 900 were only available in 1964.
View and Download Yamaha KODIAK 450 owner's manual online. KODIAK 450 Offroad Vehicle pdf manual download. Also for: Yfm450fas. Yamaha yfm 450 kodiak manual 2016. Max Motosports Starter Solenoid Relay Yamaha YFM 350/400/450/660 Grizzly Kodiak Raptor 2.9 out of 5 stars 234. 2001-2012 Yamaha Raptor 660 700 ATV Quad HAYNES REPAIR MANUAL. Published on February 20, 2016.
Later, Briska 900 and 1300 and the Contessa 1300 sedan are assembled in Haifa as well. During the many years 1964-1965, Israel had been Hino's 2nd most significant marketplace for their Contessas. Israel exports amounted to 10percent of total Contessa manufacturing. After it had been purchased by Toyota, the contract was ended and also the extremely last Israeli Contessas rolled off the assembly-line in March 1968. Altogether, over 8,000 Hino Contessa and Briska had been put together in Israel. The Hino Profia are a heavy responsibility cab-over vehicle produced by Hino Motors.
In many export areas, it is merely referred to as Hino 700. The name Profia is formally used in Japan, and was once known as the Super Dolphin Profia.
The Hino F-Series vehicle's model codes is FN, FP, FR, FS, and FW. The tractor mind design rules are SH and SS. Super Dolphin (1981-1992) Hino Super Dolphin Introduced in 1981, the Super Dolphin had been Hino's entry in to the heavy-duty vehicle marketplace in Japan, and exported internationally. Super Dolphin Profia (1992-2003) Hino Super Dolphin Profia Diesel engine availabilities is 7,961 cc J08C, 10,520 cc P11C, 13,267 cc K13D, 19,688 cc F20C, and 20,781 cc F21C. Systems FQ Length - 11.99 m (472.0 in) Circumference - 2.49 m (98.0 in) Height - 3.64 m (143.3 in) FR SH Length - 6.05 m (238.2 in) Circumference - 2.49 m (98.0 in) Height - 2.78 m (109.4 in) Profia In 2003 it had been rebranded as Hino Profia whilst still being produced in Japan without Super Dolphin badge.
The cabin design resembles the fourth generation Ranger, but the Profia are bigger. Its on the basis of the Grand Aerotech Design technology ensuing outstanding aerodynamic overall performance.
Hino Truck Wiring Diagram
The cabin in addition adopts enhanced disaster Guard effects protection (EGIS) to guard occupants. The Hino 700 is also for sale in Taiwan and made by Kuozui Motors, and it is being assembled for other stores.
Hino Manual Regeneration
The model functions 10.5-liter P11C, and 12.9-liter E13C diesel engines. Transmission is either 7, 12, or 16 speeds manual. The professional change 12 automated transmission emerges the domestic markets. The 700 can be purchased in Australia and unique Zealand with Eaton Fuller RoadRanger Super18 transmissions, since this is the most common heavy-duty transmission in use downunder. In April 2017, this facelifted version ended up being uncovered with an optional of an 8.9-liter A09C diesel motor. The manual and professional change automatic transmissions is still provided.