Trane Rtwa Service Manuals
NOTICE: Warnings and Cautions appear at appropriate sections throughout this literature. Read these carefully. WARNING: Indicates a potentially hazardous situation which, if not avoided, could result in death or serious injury.
CAUTION: Indicates a potentially hazardous situation which, if not avoided, may result in minor or moderate injury. It may also be used to alert against unsafe practices.
CAUTION: Indicates a situation that may result in equipment or propertydamage only accidents. Important - Read This First! This manual is intended for experienced service personnel familiar with the proper use of electrical diagnostic instruments and all personal safety procedures when working on live electrical circuits. This Manual is not intended for individuals who have not been properly trained in handling live electrical circuits. Environmental Concerns! Scientific research has shown that certain man-madechemicals can affect the earth’s naturally occurring stratospheric ozone layer when released to the atmosphere. In particular, several of the identified chemicals that may affect the ozone layer are refrigerants that contain Chlorine, Fluorine and Carbon (CFCs) and those containing Hydrogen, Chlorine, Fluorine and Carbon (HCFCs).
Not all refrigerants containing these compounds have the same potential impact to the environment. Trane advocates the responsible handling of all refrigerants— including industry replacements for CFCs such as and HCFCs and HFCs. Responsible Refrigerant Practices! Trane believes that responsible refrigerant practices are important to the environment, our customers, and the air conditioning industry.
All technicians who handle refrigerants must be certified. The Federal Clean Air Act (Section 608) sets forth the requirements for handling, reclaiming, recovering and recycling of certain refrigerants and the equipment that is used in these service procedures. In addition, some states or municipalities may have additional requirements that must also be adhered to for responsible management of refrigerants.
Know the applicable laws and follow them. WARNING Contains Refrigerant! System contains oil and refrigerant under high pressure. Recover refrigerant to relieve pressure before opening the system.

See unit nameplate for refrigerant type. Do not use non-approvedrefrigerants, refrigerant substitutes, or refrigerant additives. Failure to follow proper procedures or the use of non-approvedrefrigerants, refrigerant substitutes, or refrigerant additives could result in death or serious injury or equipment damage. 2 RLC-SVD03A-EN. Contents General Information. 4 Service Philosophy.
4 System Description. 5 System Level Components. 5 Interprocessor Communications. 8 IPC Diagnostics.
8 Troubleshooting Modules Using IPC Diagnostics. 9 Troubleshooting Procedure. 12 Temperature Sensor Checkout. 15 Temperature Sensor Checkout Procedure. 15 Compressor Operation. 19 Restart Inhibit Timer. 19 Compressor Start/Stop.
20 Variable Speed Inverter/Condenser Fan Control. 21 Outdoor Air Temperature and Fan Control. 22 VSF Inverter Fault. 22 Current Transformer. 23 CT and MCSP Compressor Current Input Checkout Procedure. 24 Under-Over Voltage Transformer.
32 Under-Over Voltage Transformer Checkout. 32 Compressor Capacity. 34 Checkout Procedure for MCSP Load/Unload Outputs.
Following postdoctoral work at Harvard and military service, he was appointed to the chemistry faculty of the University of Virginia in 1966. Carey and sundberg solution manual.
35 Checkout Procedure for the Slide Valve and Load/ Unload Solenoids. 36 Checkout Procedure for MCSP Step Load Output. 39 Checkout Procedure for Step Load Solenoid Valve and Piston. 40 Module Power and Miscellaneous I/O. 41 Power Supply.
41 Clear Language Display (CLD) 1U6 Keypad Overview. 42 Chiller Module (CPM) (1U1). 46 Options Module (CSR) (1U2). 50 Electronic Expansion Valve Module (EXV) (1U3). 58 Compressor Module (MCSP) (1U4 AND 1U5). 72 Interprocessor Communication Bridge Module (IPCB) (1U7). 78 LonTalk® Communications Interface - Chillers Module (LCI-C) (1U8).
79 Variable Speed Fan System. 80 Inverter Diagnostics.
80 Troubleshooting Procedure. 82 Other Service Features.
Trane Rtaa Chiller Manual
85 Service Pumpdown. 85 Circuit Lockout. 87 Circuit Diagnostic Reset. General Information The Unit Control Modules (UCMs) described in this troubleshooting guide provide a microprocessor based refrigeration control system, intended for use with Trane 70-125ton helical rotor chillers. Six types of modules are used, and throughout this publication will be referred to by their abbreviations or their Line Wiring Drawing Designations, see Table 1. Table 1 Unit Control Module Designations Line Drawing Controller Name Abbrev. Designation Chiller Module CPM 1U2 Options Module CSR 1U3 Expansion Valve Module EXV 1U4 & 1U5 Compressor Module MCSP A & B 1U6 Clear Language Display CLD 1U7 Interprocessor IPCB Communications Bridge (Remote Display Buffer) Service Philosophy With the exception of the fuses, no other parts on or within the modules are serviceable.
The intent of the troubleshooting is to determine which module is potentially at fault and then to confirm a module problem. This is done either through voltage or resistance measurements at the suspected input or output terminals or by checking related wiring and external control devices (connectors, sensors, transformers, contactors etc.) in a process of elimination.
Once a problem has been traced to a module, the module can be easily replaced using only basic tools. In general, all dip switch settings of the replaced modules should be copied onto the replacement module's dip switches before applying control power. CPM replacement is more involved as there are numerous configuration and set-upitems that must be programmed at the Clear Language Display in order to insure proper unit operation.
It is helpful to include with the return of a module, a brief explanation of the problem, sales office, job name, and a contact person for possible follow-up.The note can be slipped into the module enclosure. Early and timely processing of Field Returns allows for real measurements of our product quality and reliability, providing valuable information for product improvement and possible design changes. General Information System Description The CPM is the master module and coordinates operation of the entire system. One is used per chiller. The MCSP is a compressor protection module with one being used for each of the compressors in the chiller. The EXV is the expansion valve controller module which controls two Electronic Expansion Valves. There is one valve on each of the two refrigeration circuits.
The CLD is a two line, 40 character alphanumeric interface to the system. It allows the operator to read operating and diagnostic information, as well as change control parameters. The Interprocessor Communications Bridge (IPCB) provides an extension of the IPC link to the Remote Clear Language Display, while protecting the integrity of the IPC communications link between the local modules. The CSR is an optional communications module which allows for communications between the chiller and a remote building automation system (i.e. Tracer, Tracer Summit, Generic BAS).
All modules in the system communicate with each other over a serial interprocessor communications bus (IPC) consisting of a twisted wire pair “daisy chain” link and RS485 type signal levels and drive capability. Multiple modules of the same type (i.e.
MCSPs) in an operating system are differentiated by address dip switches. All the modules operate from 115VAC, 50 or 60Hz power and each have their own internal step-downtransformer and power supply. Each is individually fused with a replaceable fuse. The modules also are designed to segregate their high and low voltage terminals by placing the high voltage on the right side of the module and the low voltage on the left. When stacked, segregation is maintained. In addition to the modules, there are a number of “system level” components that are closely associated with the modules. These components were specifically designed and/or characterized for operation with the modules.
For this reason, the exact Trane part must be used in replacement. System Level Components Description The following is a list of all the components that may be found connected to the various modules. Transformer, Under/Over voltage Current Transformer - Compressor Evap EntlLvg Water Temp Sensor Pair Sat Evap/Cprsr Suc Rfgt Temp. Sensor Pair Sat Cond RfgtIOil Temp Sensor Pair Outdoor Air Temperature Sensor Zone Temp Sensor Connector (UCM mating connectors) Connector Keying Plug Electronic Expansion Valve. General Information High Pressure Cutout Switch Low Pressure Cutout Switch Variable Speed Fan Drive Motor Temperature Thermostats Slide Valve Load/Unload Solenoids Step Load Solenoid Valve Chiller Module (CPM) IU1 The CPM module performs machine (chiller) level control and protection functions. Only one CPM is present in the chiller control system.
The CPM acts as the master controller to the other modules, running top level machine control algorithms, initiating and controlling all inter-modulecommunication over the IPC, and providing parameters and operational requests (i.e. Loading and unloading, starting and stopping) to the other modules in the system via the IPC. The CPM also contains nonvolatile memory, which allows it to remember configuration and set-upvalues, setpoints, historical diagnostics etc. For an indefinite period of time following a power loss. Direct hard wired I/O associated with the CPM includes low voltage analog inputs, low voltage binary inputs, 115 VAC binary inputs and 115 VAC (rated) relay outputs. See Chiller Module (CPM) (1U1) on page 46 for further details.
Compressor Module (MCSP) 1U4 and 1U5 The MCSP module employs the input and output circuits associated with a particular compressor and refrigeration circuit. Two MCSP modules are used in the UCM system, one for each compressor.
Included are low voltage analog and digital circuits, 115 VAC input, and 115 VAC output switching devices. The output switching devices associated with the compressor motor controlling function are contained in this module. The outputs of this module control one compressor motor stop/start contactor, one compressor motor transition contactor, one oil heater, three solenoid valves (compressor load, compressor unload, step loader), and up to four fan motor contactors or groups of contactors. Refer to the chiller's line wiring diagrams for details.
Dip switches are provided for redundant programming of the compressor current overload gains, and for unique IPC address identification during operation. Inputs to this module include motor temperature thermostats, thermisters, and safety switches. See Compressor Module (MCSP) (1U4 AND 1U5) on page 72 for details. Expansion Valve Module (EXV) 1U3 The EXV module provides power and control to the stepper motor driving the electronic expansion valves of the chiller.
Each module handles two valves, one in each refrigeration circuit. Input to the EXV Module is provided by four temperature sensors (two per refrigeration circuit).
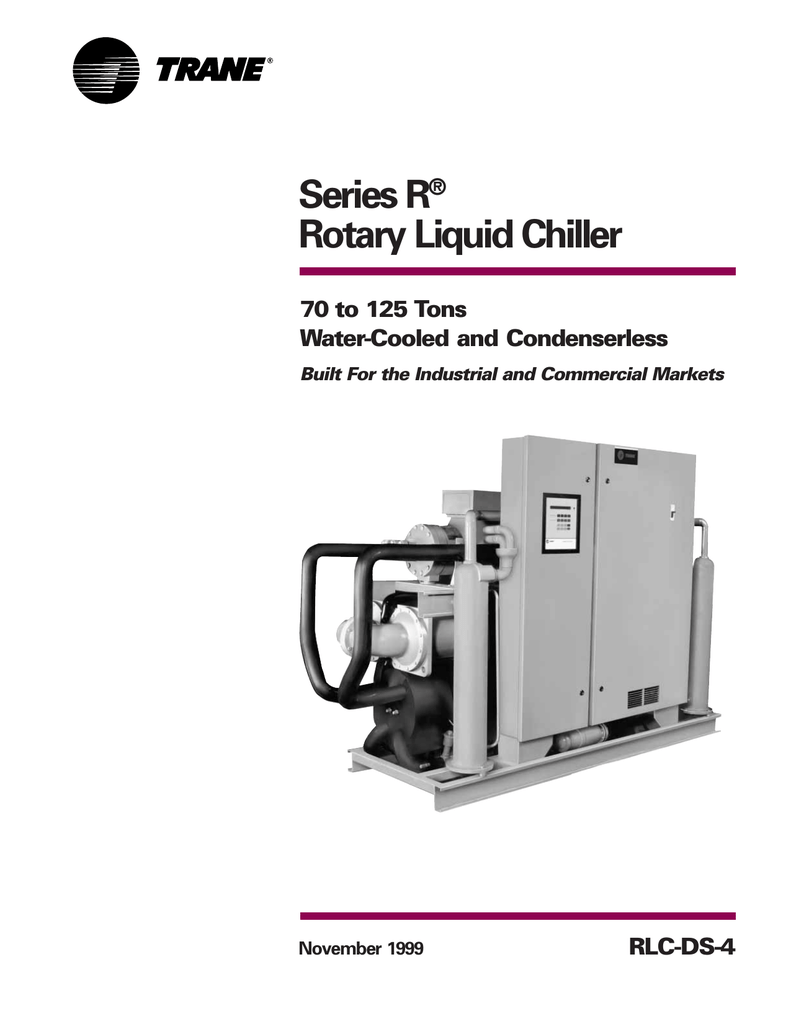
The sensors are located in the respective refrigeration circuits of the chiller and sense Saturated Evaporator and Suction temperatures and calculate the superheat temperatures. High level operational commands as well as superheat setpoints are received by the EXV Module over the IPC from the CPM module to modulate the EXV's. General Information Real time data for temperatures, diagnostics and control algorithms etc. Are made available to the CPM and the other modules for display and for input to higher level functions.
See Electronic Expansion Valve Module (EXV) (1U3) on page 58 for details. Options Module (CSR) 1U2 The CSR module is an optional part of the system and employs communications circuits for interface to Trane Building Automation Systems, done through 1C17. The CSR also provides inputs for hard wired external setpoints and reset functions. Included are low voltage analog and digital input circuits. See Options Module (CSR) (1U2) on page 50 for details. Clear Language Display (CLD) 1U6 The CLD Module provides an operator interface to the system, through a two line, 40 character alphanumeric display. Three reports may be displayed and various operating parameters may be adjusted by depressing a minimal number of keys on the CLD.
Also, chiller Start/Stop functions may be performed at this keypad. See Clear Language Display (CLD) 1U6 Keypad Overview on page 42 for details.
Interprocessor Communication Bridge (IPCB) 1U7 The IPCB module allows connection of a Remote Clear Language Display module to the UCM, for distances of up to 1500 feet. The Remote Clear Language Display communicates with the UCM, utilizing the same IPC protocol, and provides most of the same functions as the local CLD. The IPCB then serves to protect the UCM's IPC if wires to the Remote CLD become shorted or broken. See Section 2 and on page 75 for details.
Interprocessor Communications The respective modules communicate with each other via an InterProcessor Communication link (IPC). The IPC allows the modules to work in a coordinated manner with the CPM directing overall chiller operation while each module handles specific subfunctions. This IPC link is integral and necessary to the operation of the Unit Controls and should not be confused with the Optional ICS (Integrated Comfort System) communication. In the IPC communication protocol scheme, the CPM acts as the initiator and the arbitrator of all module communication. The CPM essentially requests all the possible “packets” of information from each module in turn, (including itself), in a predefined serial sequence.
The other modules act as “responders” only and cannot initiate communication. Modules which are not currently responding to a specific request, can listen to the data and thus, indirectly, they communicate with each other. It is helpful to remember when troubleshooting that a module must be able to hear a request for its information from the CPM, or it will not talk. The link is non-isolated,which means that a good common ground between all the modules is necessary for trouble-freeoperation (provided by the module enclosures' mounting using star washers). Also, the link requires consistent polarity on all of the module interconnections.
Connections between modules are made at the factory, using unshielded #18 gauge twisted pair cable terminated into a 4-positionMTA type connector (orange color code). This connector is plugged onto the 4 pin IPC connection jack designated as J1, located in the upper left corner of the PC board edge on all of the modules.
The 4 pins actually represent 2 pairs of communications terminals (J1-1(+) internally connected to J1-3,and J1-2 (-)internally connected to J1-4)to allow for easy daisy chaining of the bus. IPC Diagnostics The modules, in order to work together to control the chiller, must constantly receive information from each other over the IPC. Failure of certain modules to communicate or degradation of the communication link, could potentially result in chiller misoperation. To prevent this situation, each module monitors how often it is receiving information from designated other modules. If a module fails to receive certain other module's transmitted data over a 15 second time period it will: 1. On its own, take specific action to safely shut-down(or to default) its controlled loads.
Report a diagnostic to the CPM (over the IPC link). The CPM (if it properly receives such) will then report and display the diagnostic on the Clear Language Display accordingly.
The diagnostic will:. identify which module is reporting the communication problem and. identify which module was to have sent the missing information. The CPM itself will then send out further commands to the other modules to shutdown or take default actions as the particular case may warrant. All IPC diagnostics are displayed in the Clear Language Display's diagnostics section.
For example, “Chiller Mod indicating Options Mod Comm Failure” indicates that the CPM Module has detected a loss of IPC communication. Interprocessor Communication from the Options Module. When some problem exists with the IPC link or a module fails, it is not uncommon for more than one of these IPC diagnostics to be displayed.
Note that only those diagnostics that are indicated to be active currently exist. All other historic diagnostics should be disregarded for the purpose of the following troubleshooting discussion. See RTAA-IOM-4for a complete listing of diagnostics. Troubleshooting Modules Using IPC Diagnostics WARNING Live Electrical Components! During installation, testing, servicing and troubleshooting of this product, it may be necessary to work with live electrical components. Have a qualified licensed electrician or other individual who has been properly trained in handling live electrical components perform these tasks.
Trane Helirotor Compressor
Failure to follow all electrical safety precautions when exposed to live electrical components could result in death or serious injury. Communication problems can result from any of the following: 1. Improperly set IPC address dip switches 2. Opens or shorts in the twisted pair IPC wiring or connectors 3. Loss of power to a module 4. Internal module failure 5.
Improper connections on terminal J2 6. High levels of EMI (Electro-MagneticInterference) 7.
Module specific function selected without the Options Module. These are discussed in more detail in the following paragraphs.
Improperly set IPC address dip switches: This could result in more than one module trying to talk at the same time, or cause the mis-addressedmodule to not talk at all. Only the MCSP and the EXV modules have IPC address dip switches, found in the upper left hand portion of the Module labeled as SW-1.The proper dip switch setups are shown in Table 2. Opens or shorts in the twisted pair IPC wiring or connectors: One or more modules may be affected by an open or a short in the IPC wiring, depending on the location of the fault in the daisy chain. The diagram below shows the daisy chain order and is helpful in diagnosis of an open link. Extreme care should be used in making any dip switch changes or when replacing MCSP modules.
“Swapping” of addresses on the MCSPs cannot be detected by the communication diagnostics discussed above and serious chiller misoperation will result.